Sub-Slab Leak Repair Stockton
Residential slab leak detection & repairs in the Central Valley.
With one of California’s largest concentrations of slab-foundation homes, the Central Valley experiences its fair share of slab leaks.
Our repair process begins by setting up containment in the same meticulous manner as a surgical team preparing an operating room. We use zip-wall containment to prevent dust and debris from spreading throughout the house.
To avoid damaging post-tension slab cables, we start by scanning the concrete and marking any potential cable locations. We then jackhammer the ground open and excavate it, removing gravel and soil from under the slab to expose the buried copper piping. Our technician cuts out the leaking section of the copper pipe.
Often, the leak is as small as a pinhole or the tip of a ballpoint pen. Once the leak is removed, we test the system in both directions to check for any additional leaks in the affected area before making the repair. Our technician then repairs the copper piping under the slab and conducts a final pressure test. Typically, our technician will back-fill and patch the concrete, smoothing and leveling it to match the existing slab.
As a leading sub-slab leak repair company in Stockton, we guarantee our repairs with a one-year warranty.
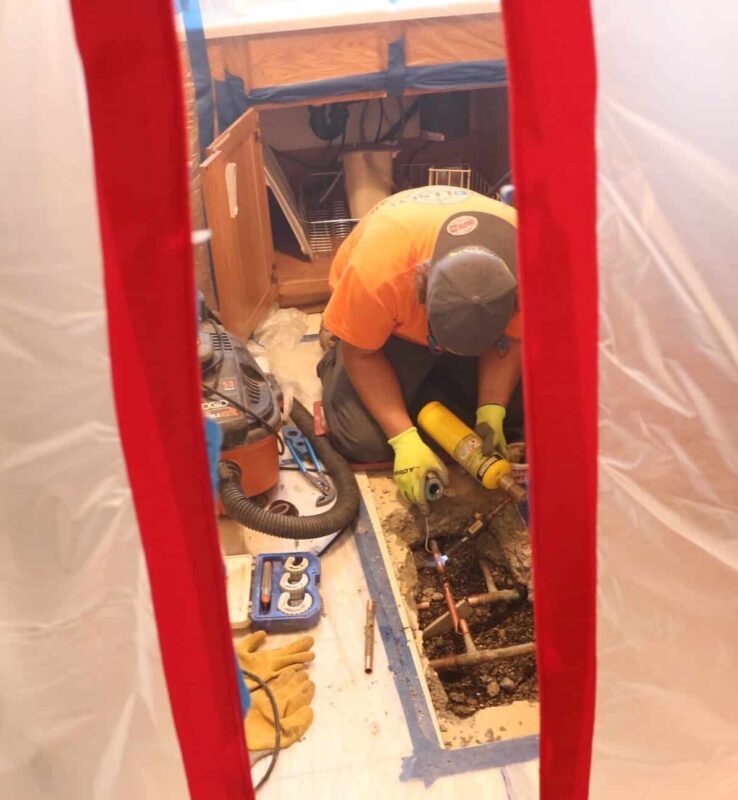
Types of sub-slab piping
Soft-rolled copper pipe | steel water pipe | copper hard pipe
The sub-slab copper piping that is most common is a soft-rolled copper pipe, installed in the ground before the concrete is poured. It was used for many years because it allowed plumbers to lay long sections of pipe across the house without slowing down the construction process.
Soft-rolled copper also enabled the installation of pipe lengths without connecting fittings under the slab. Each end of the copper pipe would rise into the wall and connect to the supplied fixture, as well as to additional piping feeding other fixtures. This connection point is typically referred to as a manifold (see photo B).
Homes built before the mid-1970s often used an outdated building practice where pipes were installed under the slab with below-grade fittings feeding each fixture or additional location. This often resulted in broken sub-slab fittings (see photo A). Some of these homes were plumbed under the slab with steel water piping, while others used copper hard pipe. Our technician can usually identify the piping layout during the initial inspection. The only repair options for sub-slab hard pipe are to excavate the leaking location and replace a small section of the pipe or abandon the underground piping and repipe overhead.
Sub-Slab Construction
Concrete-slab homes are still made these days but current building codes require a chase pipe or conduit surround the piping and transition fittings must be located above grade.
Most residential concrete slabs are between 3 and 10 inches thick. The perimeter of the home and the load-bearing areas are typically 2-3 feet thick. The concrete is poured all at once to create a continuous connection between the concrete floor and the foundation.
Before pouring the concrete, contractors and plumbers install the sewer and water pipes at a depth of approximately 12 inches to 4 feet. This piping is positioned to align with the planned locations of the plumbing fixtures.
Usually, the contractor places a Visqueen waterproof barrier and then a layer of gravel before pouring the concrete. As a result, homeowners often do not see moisture or water surfacing in the home from an underground slab leak, as the water drains into the ground and away from the home.
Call or request sub-slab leak repair Stockton services online!